SeasonedBeef
Student
Here is a project that I've been working on from scratch for the past two years. It's actually quite far along already in the build phase! Just two more pieces to print and assemble.
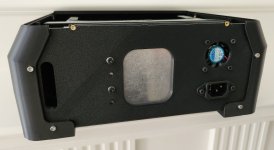
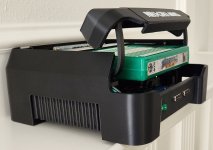
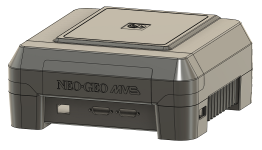
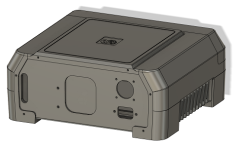
Design goals and constraints:
I have to pause here for now. I'll make some more updates going into a bit more detail on the internal layout, cooling, some of the trade-offs I had to make, and then some of the build process.
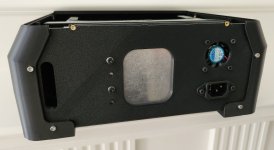
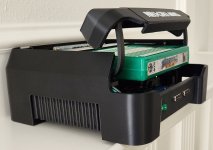
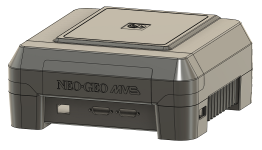
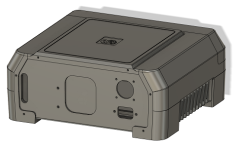
Design goals and constraints:
- It needs to look and function like an actual console from the 90's
- Frontload like an NES with a top hinged cartridge door. The hinge needs to be hidden if possible.
- It has to be simple to change games.
- The plastic SNK branded cartridge guide that comes with the MV1B must be used. It will be built in to the structure.
- 3D printed using ABS, including the logos. 300mm^3 printer max size.
- Use the Minigun Supergun with no deviations. Plug and play. RGB out only.
- Internal PSU. The back panel will have a 120V AC female socket, just like a PC.
- All electronic components were readily available and sourced from Digikey. No custom PCB's (other than the minigun).
- Absolutely no modifications needed to the MVS board. The only soldering I did was to make the minigun.
- Front mounted, illuminated power switch to the A/C input of the rear power supply.
- Finally, maybe most importantly, show the underappreciated MV1B board some love for what it is, and not just flatten it into a toploader configuration.
I have to pause here for now. I'll make some more updates going into a bit more detail on the internal layout, cooling, some of the trade-offs I had to make, and then some of the build process.